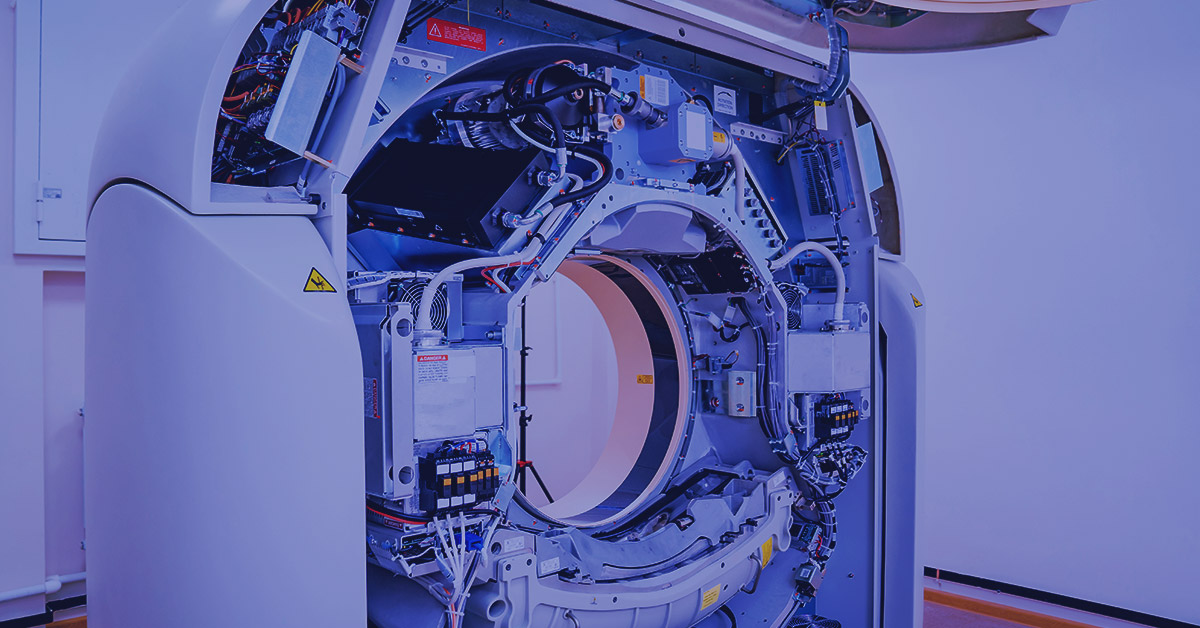
The Evolution of Medical Device Service
Medical equipment manufacturers have managed device support through various processes and systems over the years. This blog summarizes elements of a modern service model and associated support processes.
Modern Medical Device Servicing and Maintenance
With the increasing complexity of electronic devices, the use of surface mount technology, and the miniaturization of components, it has become more challenging to perform component level troubleshooting and repair. Many electronic devices are now designed with highly integrated circuits, where a single faulty component may require the replacement of the entire circuit board. In addition, some manufacturers now use automated assembly processes that make it difficult to replace individual components. While software and computers have gained importance, the age of soldering rod and component level troubleshooting is not entirely over, but it is certainly diminishing.
This has ushered in an era of functional block level troubleshooting and equipment maintenance. As early as about ten years ago there were entire cabinets dedicated to a particular operational or engineering function in an MRI or CT scanner. Today, these complex functions are largely effected via one or two LSI (large Scale Integrations) and dedicated functional chipsets. Increased density of function leads to increased co-dependence and complexity of components. This increases the need for more software aided troubleshooting and calls for effective parsing of error codes that may be generated by these chips. The age of “hunt and peck” for defective components to troubleshoot a malfunction is largely history.
Today, most equipment generates a complex variety of logs and live status reports. The sheer volume, variety and velocity of such machine logs require a rethink in terms of human interaction with this data. Tools that are able to quickly analyze and visually depict fault areas and deficiencies in the operation of the equipment are the need of the hour. Many large manufacturers have dedicated software aided tools and computer-based documentation to aid in rapid troubleshooting and maintenance.
Organizations can create knowledge bases by documenting existing knowledge in various formats such as manuals, reports, case studies, and best practices. This can be done by subject matter experts or by dedicated knowledge management teams. Other methods can be by leveraging the collective knowledge of their employees, customers, or other stakeholders to create knowledge bases. This can be done through online platforms such as wikis or forums, where users can contribute, edit, and collaborate on knowledge articles.
Computer-based documentation and digital tools for service are typically faster and more efficient than traditional paper-based documentation and troubleshooting strategies. Accessibility, Accuracy and Security of digital tools help streamline communication and reduce errors.
With large scale computer-based data generation required for support services, manufacturers need to use a variety of knowledge management systems to capture and share technical knowledge with their support team and customers. This is not only imperative given the amount of information that needs to be processed but also improves the efficiency of problem-solving and reduces the time required to resolve issues. Such a knowledge management system can not only drive a steady state knowledge creating organization, but improved reliability and uptime for endusers.
Today, data is ubiquitous and data mining techniques are available to extract insights and knowledge from large amounts of data. This can be done through tools such as machine learning algorithms or natural language processing. Expert systems could be developed with such tools which are computer-based systems that emulate the decision-making abilities of a human expert in a specific domain.
Medical Device Service Personnel and Equipment
Most medical imaging systems are still supported by Field service technicians providing on-site support and performing preventive maintenance, repairs, and installations. These technicians can be dispatched based on the equipment’s criticality and the service level agreement with the customer. Service Contracts are offered that include preventive maintenance, software upgrades, and on-site support. These contracts can provide customers with peace of mind and ensure their equipment is maintained to a high standard.
Multiple departments and stakeholders in a typical organization are dedicated to support. These include 24×7 Help Desks and Remote Technical support structures. These provide rapid support to customers by answering their queries and providing technical assistance. Most help desk entities can be accessed through phone, email, or web-based chat systems. Remote support tools allow an engineer / technician to remotely access and troubleshoot equipment issues. This can reduce the need for on-site visits, saving time and cost.
Biomedical technicians use a variety of tools and equipment to maintain, repair, and calibrate medical equipment and devices. Depending on the need and complexity of the troubleshooting task, these tools encompass a broad array of equipment.
While hand tools such as screwdrivers, pliers, and wrenches, to disassemble, repair, and reassemble medical equipment are the most common, various types of test equipment are used to diagnose and troubleshoot problems. This may include multimeters, oscilloscopes, and other electronic testing tools.
Calibration equipment are a separate class of tools to ensure that medical equipment is operating within their specified parameters. This may include calibration weights, pressure gauges, dose measuring instruments, current and voltage measuring devices and other specialized equipment.
Biomedical technicians also use various types of safety equipment, such as gloves, goggles, and respirators, to protect themselves while working with medical equipment and devices. While often overlooked, safety wear and personnel protective devices are very critical in the domain of medical equipment. PPE and OSHA regulations are very stringent and cover a broad array of standards to be met while troubleshooting or working with medical devices.
Increasingly, both biomedical technicians and field engineers use software tools to diagnose and troubleshoot problems with medical equipment. Devices such as infusion pumps, ventilators, and dialysis machines and modern medical imaging equipment like CT scanners, MRI’s and nuclear medicine deploy complex software and hardware. Given that most modern devices are increasingly software driven and process controlled via software embedded or otherwise, the current class of biomedical technician must be familiar with usage of computers and associated peripheral devices and infrastructures. Wireless networks, Image transfer standards like DICOM, picture archiving and remote medicine, high resolution imaging equipment, routing protocols and the rapid digitization of the healthcare industry has ushered in a need for a more modern field engineer!
Explore the Possibilities
With more than 1 million exams examined each day by Glassbeam solutions, see how top organizations are transforming their log data into impactful insights.
Transform Your Healthcare Operations
See how to gain deeper, clearer insight from your machine data to elevate business intelligence and to improve your operational uptime, utilization, and efficiency.